Are you a Manufacturer?
Is aACE the Right Software for You?
Manufacturing companies can benefit from a host of capabilities and features in aACE. aACE is ideal for both high-volume “job shops” and low-volume manufacturers with long-term production orders. We generally work with our manufacturing clients to tailor workflows to their precise production requirements.
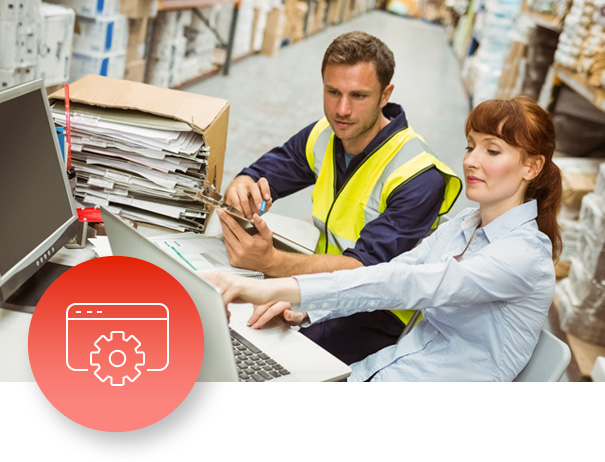
Order Entry
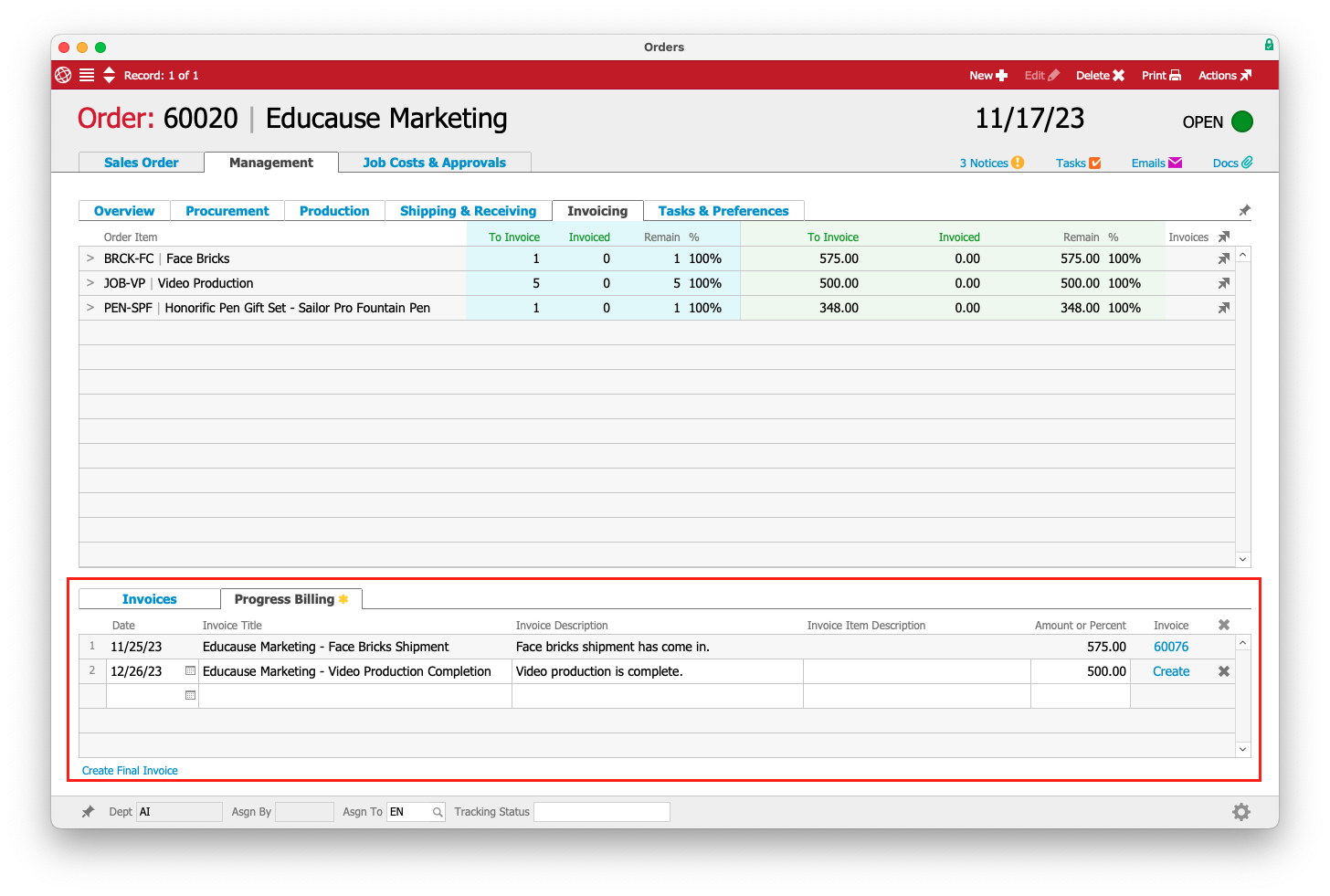
Flexible Order Creation
Build production items for made-to-stock (MTS) and made-to-order (MTO) items in a hierarchical view by selecting components from the options interface or from the master list. Costs for production include fixed and variable material costs, fulfillment (labor) costs, and component/sub costs.
Margin-based Pricing
aACE prices production items based on a margin that incorporates the full cost of the inputs: bill of material components, optional components, and fulfillment labor costs.
Progress Billing
Progress billing allows for the billing of orders in percentage or fixed-dollar installments.
Product Setup
Bill of Materials & Options
Managers can configure both bill of materials and options for assembly items. Bill of material components typically remain hidden during order entry and represent the implicit aspect of production. The options interface allows managers to specify different and custom configurations for user selection during order entry.
Bill of Operations and Manufacturing Travelers
Items in aACE can be assigned to a task group (bill of operations). A task group is a specific set of tasks (steps) that need to be taken during your standard production workflows. Each task contains information about the labor category, duration, budget, and assignment.
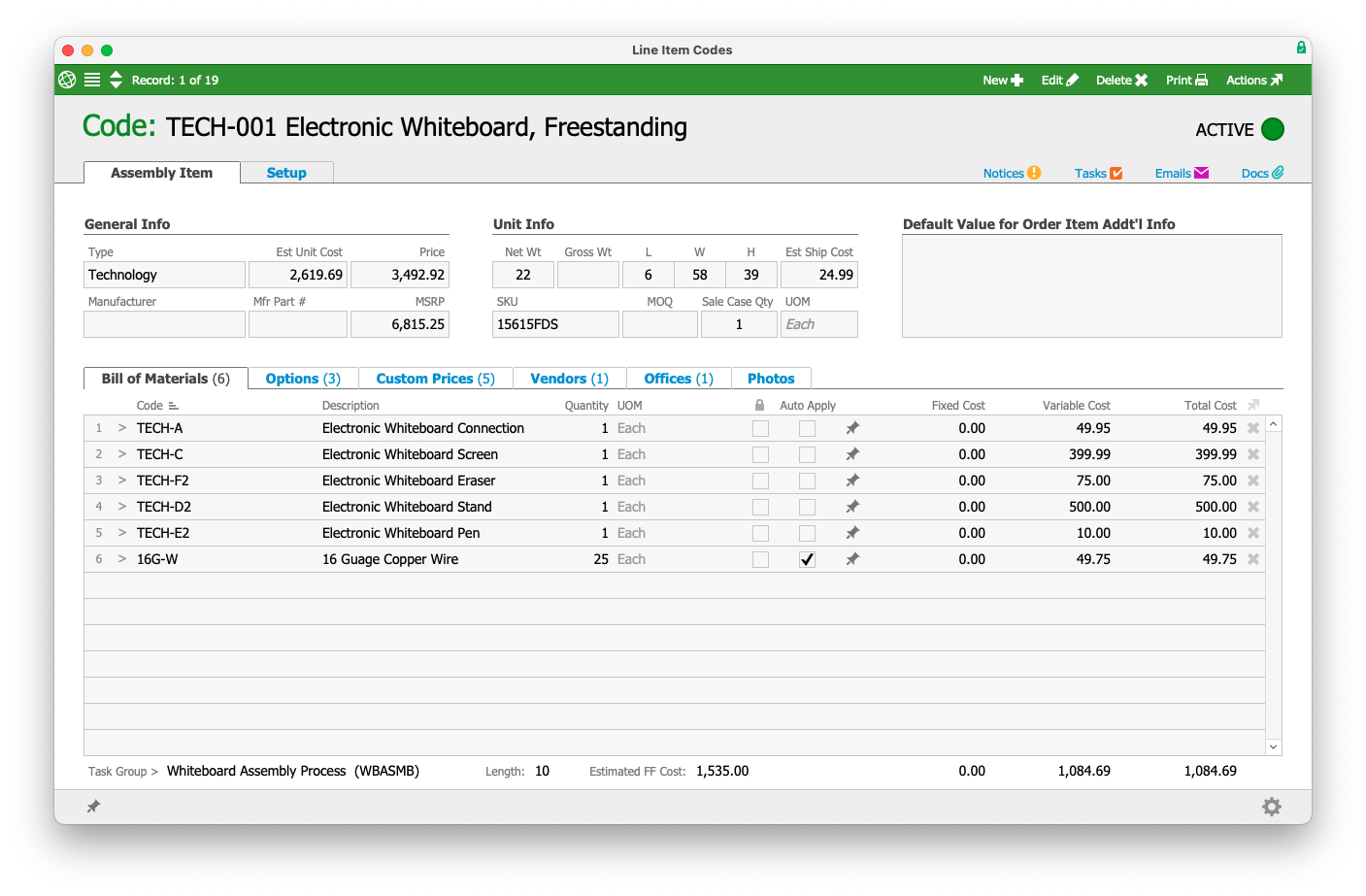
Assemblies and Jobs
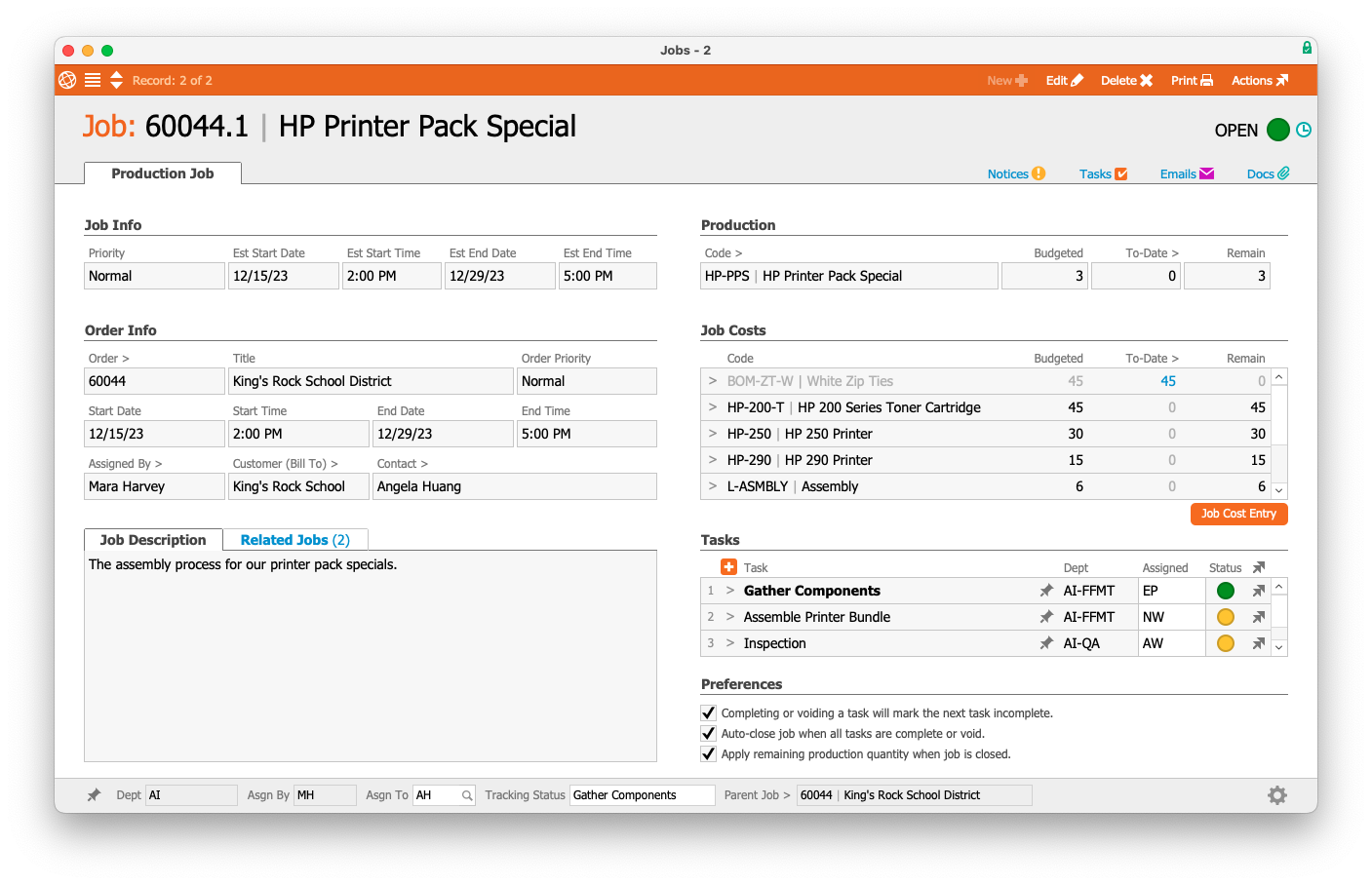
Multi-level Assemblies
aACE supports both single and multi-level assemblies. Each assembly is assigned a job number when an order is opened. The ID of the job reflects its position in the work breakdown structure (WBS).
Job and Task Scheduling
Preferences allow managers to determine whether the deepest assembly is scheduled first or last. The duration of each job is a function of the associated task group. Anchor settings within the task group and department start/stop times determine the schedule for each task.
Job Oversight and Transparency
Tracking information in the job communicates the current stage of production based on the currently incomplete task. Use of color coding immediately indicates whether a job is pending, on schedule, or past due.
Procurement
Procurement Planning
Select substitutes, keep the preferred vendor, or choose from alternative vendors for an order. Purchase orders can be generated when components are required in the production process.
Notifications
Managers are automatically sent a notification when goods are received by the receiving department. Notifications can be sent within aACE, as emails, or text messages.
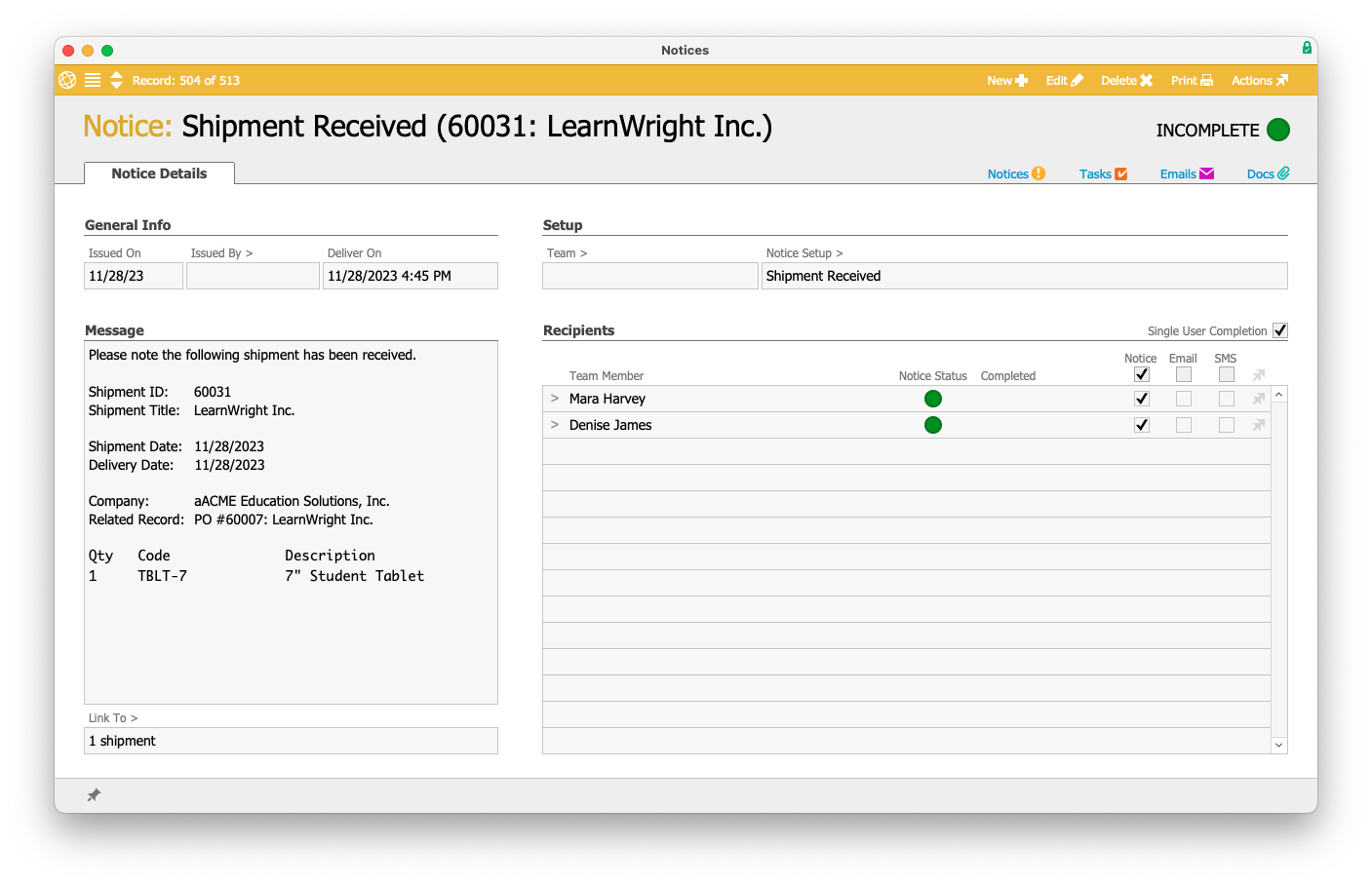
Inventory Management
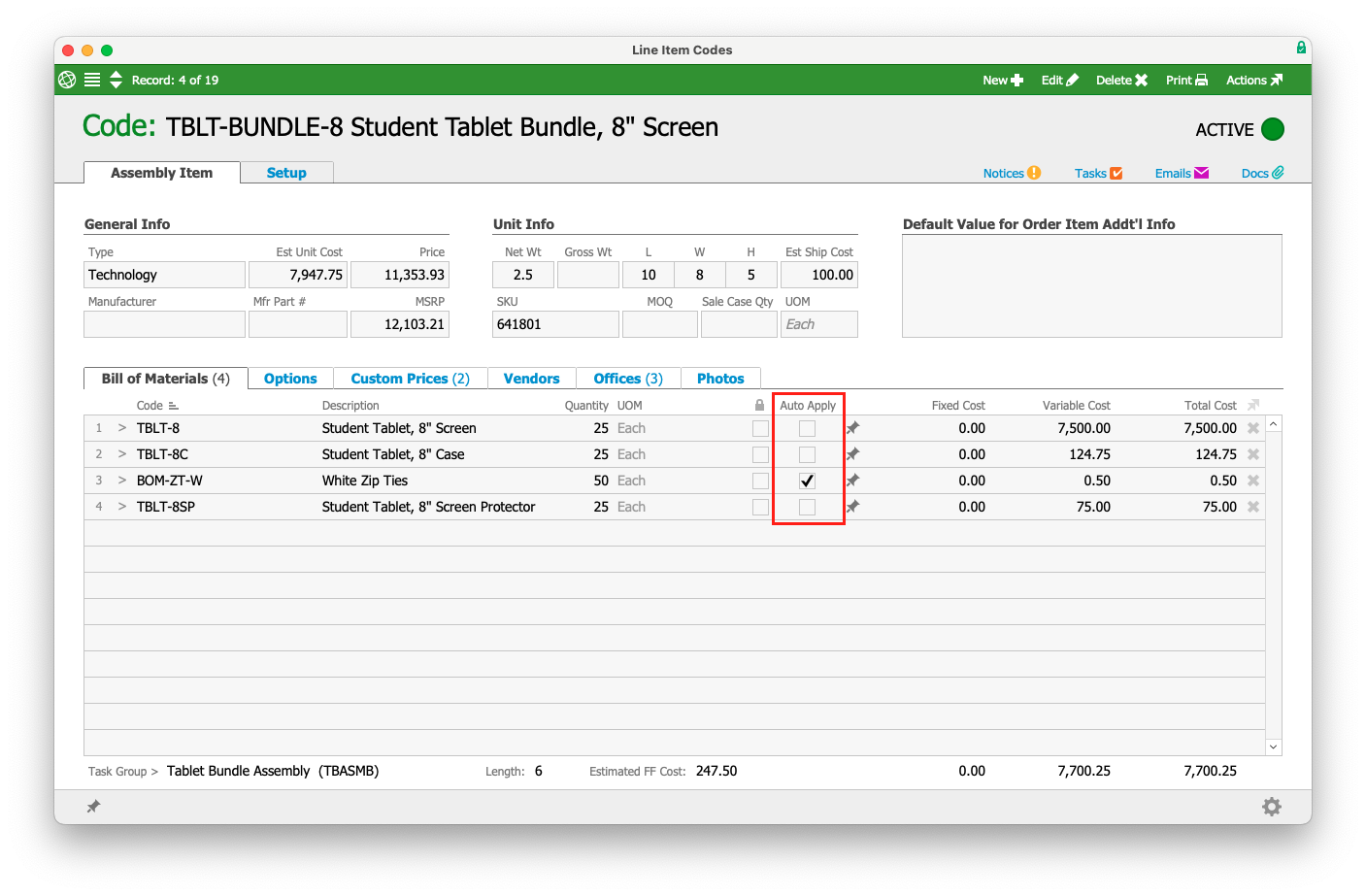
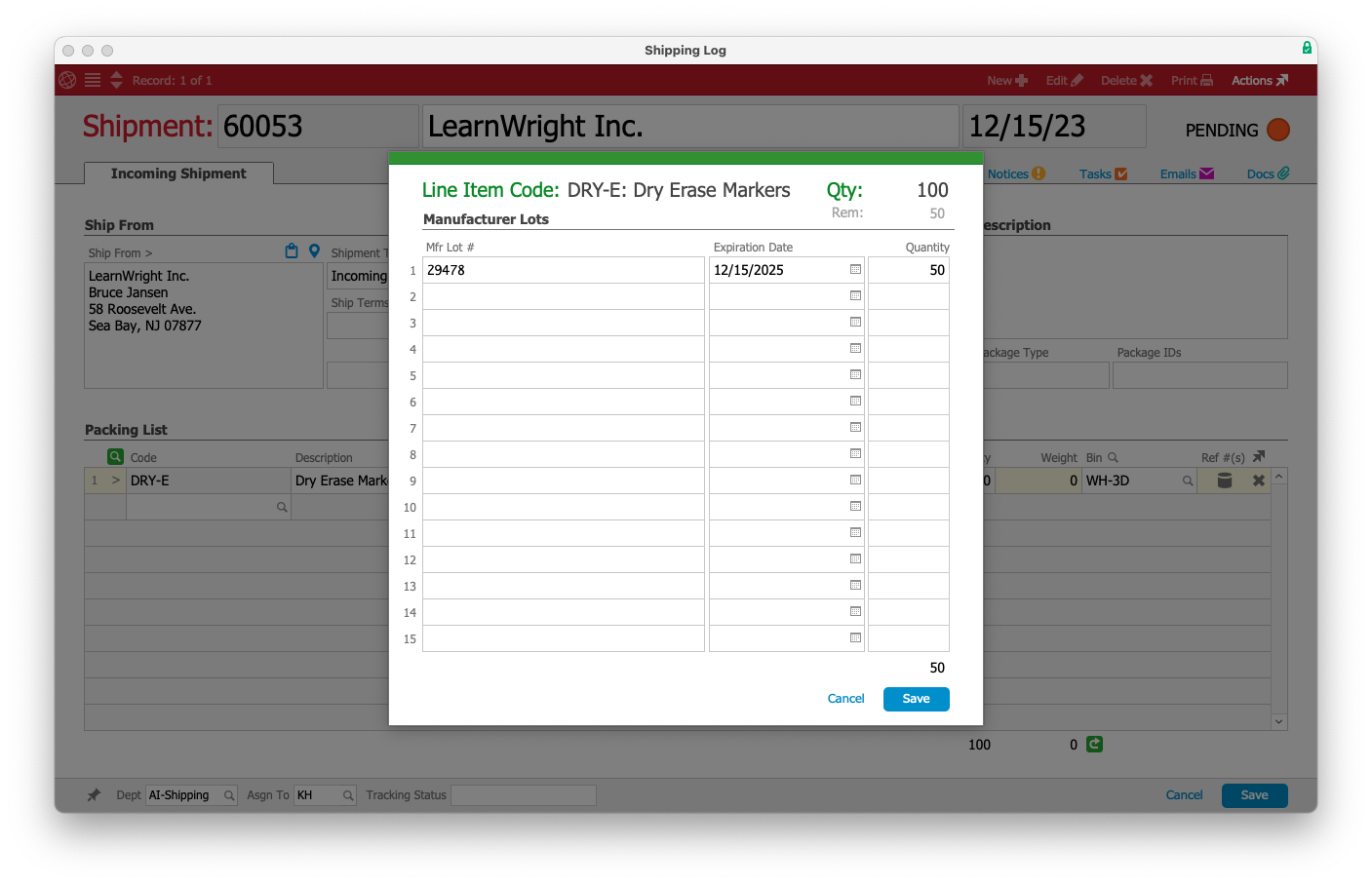
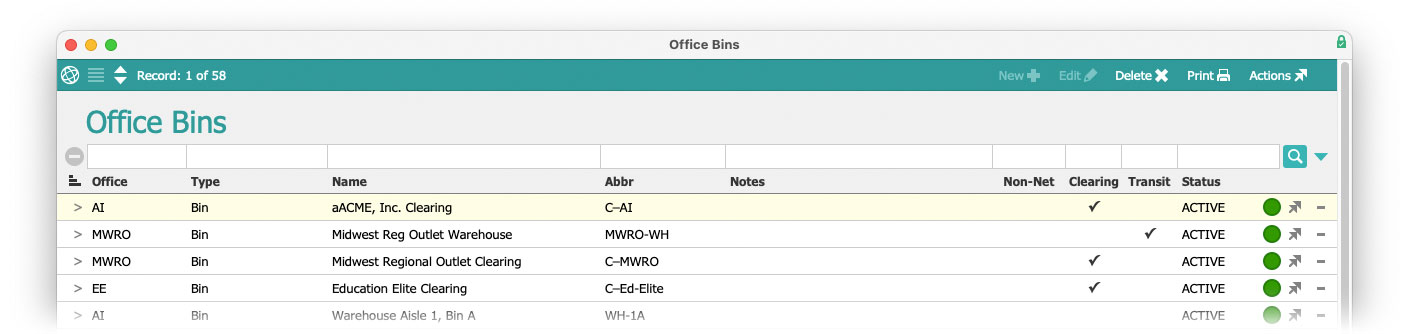
Auto-Apply Bills of Materials
Bill of material components can be flagged to auto-apply the inventory costs when inventoried item selection is either impractical or impossible. Similarly, inventoried items procured for a specific job can be auto-applied upon receipt if the goods are moved directly to the machine.
Backflush Entry
aACE supports backflush entry for assembly items, allowing job managers to simply enter exceptions at the end of the production process.
True Cost of Goods Sold
Determine the true cost of goods and create necessary GL entries. The aACE COGS process allocates inventory usage records to inventory lot records using the applicable actual cost method (e.g. FIFO, LIFO, or specific-unit logic).
SERIALIZED AND LOT-TRACKED INVENTORY
Manage inventory quality with lot and serial tracking. aACE makes it easy to manage serialized and lot-tracked items, such as electronic components and consumables.
Landed Costs and Inventory Valuation
Determine the actual margin for your products and establish proper sales prices by incorporating landed costs into your inventory value calculations.
Manage Multiple Warehouses and Trucks
aACE contains a robust bin management featureset allowing for multiple warehouses, default locations for receiving new material or returns, and transit bins for material on the move between warehouses.
Mobile Apps for Production
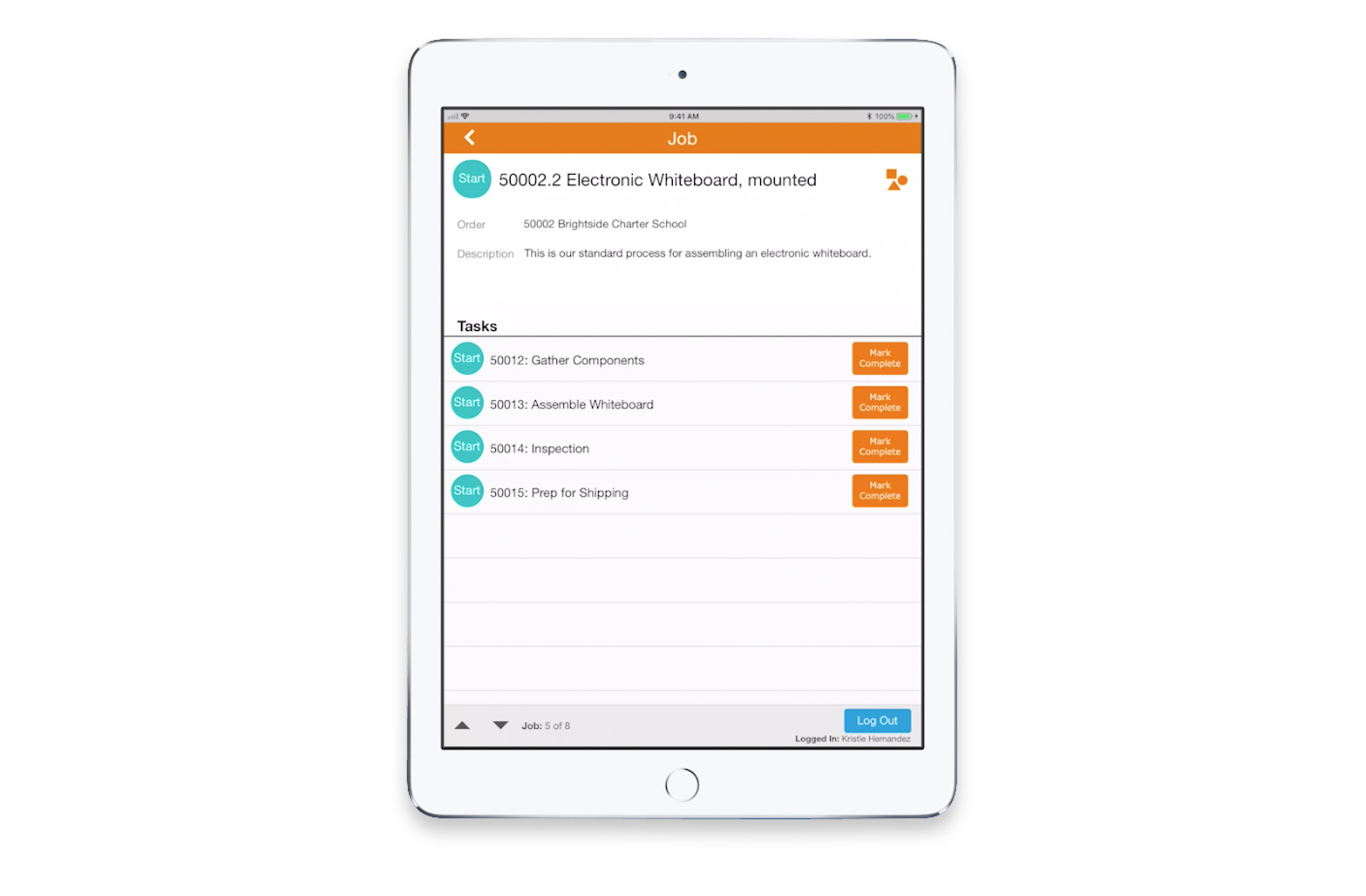
Operator Entry App
Through the Production App, operators can record inventory usage throughout the production process.
Job Shop/ Production App
In one mobile-enabled interface, implement easy-to-use shop floor time-tracking and task management.
Inventory Counting App
Warehouse team members can count inventory with an iPad and a laser barcode scanner through the aACE Inventory Mobile App.
Manufacturer Success Stories
See what aACE can do for Manufacturers
A Complete Fit for Precast Metal Manufacturer
Powering the Future: aACE and W-Industries Build aACE 6 Together
aACE Takes Plastics Manufacturer “From a Horse and Buggy to a Ferrari”
Janibell Goes Global with aACE
aACE Shines a Light on ASCENTI Lighting Operations
Closet Works Keeps Their Operations Organized with aACE
Growing Together: Duggal Celebrates 10 Years on aACE
A Stable, Proven Solution for a Fast-Paced Manufacturing Business
Gable Finds Time with aACE+ DayBack Calendar
Special EFX Runs 3 Businesses in 1 aACE Solution
Restylers’ Choice Sees Substantial ROI in 6 Months with aACE
For a Company Switching from Windows to Mac, aACE Offers Best of Both Worlds
After 30 Years in Business, Vacutherm Inc. Finds Room to Grow with Help from aACE
Redd Remedies Finds Cure for ERP Ills in aACE 5
See All Our Success Stories