Keeping up inventory levels can quickly turn into a very lengthy, manual process. You have to assess current inventory, identify how much you need to order to keep the desired quantity on your shelves, then create a purchase order for a specific vendor. But inventory replenishment doesn’t have to be this complicated.
aACE has multiple automatic inventory features that can help with managing inventory levels so you don’t have to. Based on preferences, you can set target and replenishment balances so both aACE and your team know when it’s time to restock.
Interface Spotlight
Target and replenishment balances are used to help you maintain the desired inventory levels in your warehouse. The target balance tells aACE the maximum number of items that should be kept on warehouse shelves. The replenishment balance tells aACE when to automatically generate a purchase order to bring the inventory back up.
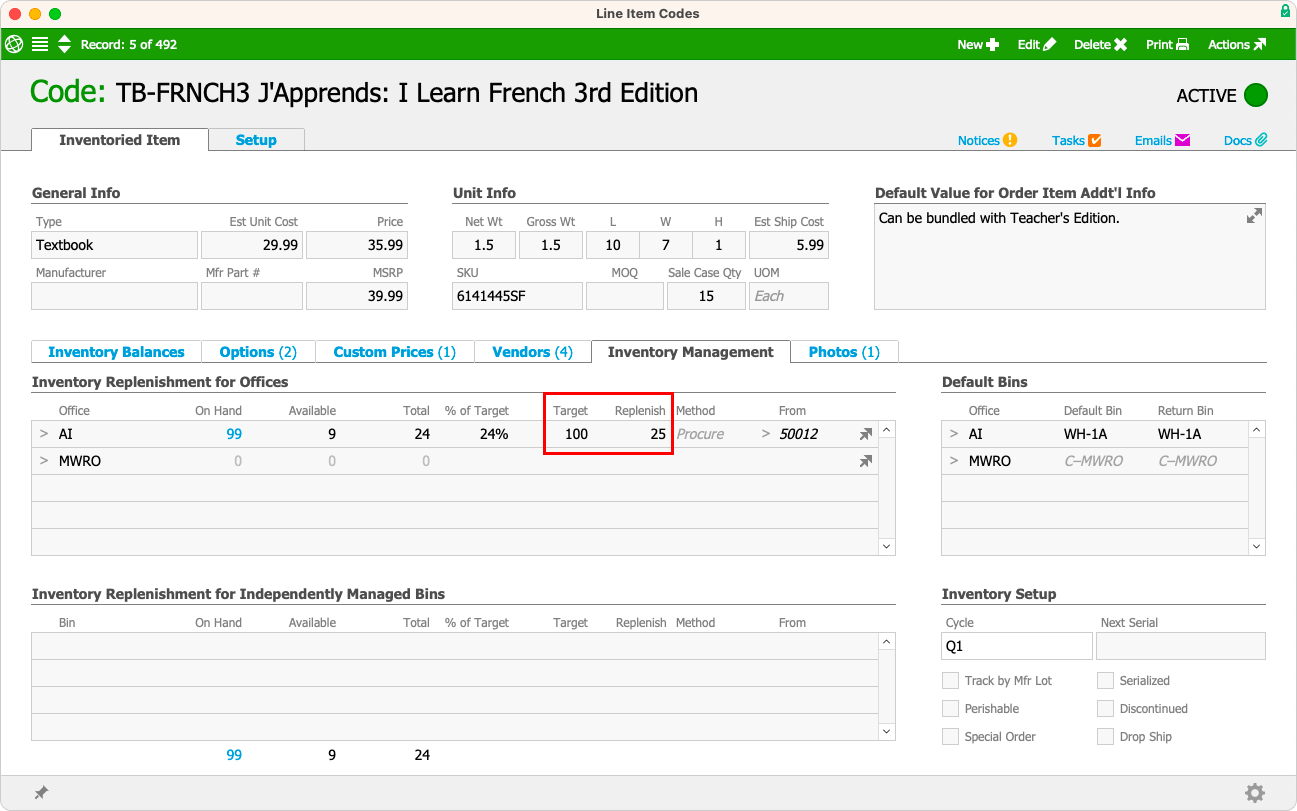
You can set inventory target and replenishment thresholds for different offices or independently managed bins, such as delivery vehicles. The detail view of a line item code (shown above) provides sections to manage these thresholds separately. If your business does not want automated inventory replenishment, aACE allows you to manually remove replenishment for individual offices and bins.
If you need to manually update your thresholds before aACE’s automatic replenishment, you can easily do that too.
Importantly, aACE can update pending replenishment purchase orders in real time through automation schedules. This preference prevents your team from having to manage multiple purchase orders to one vendor in the same day, saving on processing costs.
aACE in Action: Updates to Replenishment Purchase Order
Suppose aACE creates a new, pending purchase order (PO). The PO was initially created to replenish one item that a vendor supplies. The Generate Inventory Replenishment process runs again as part of an automation schedule, set up by your system administrator. The process finds additional items that need to be replenished and which the same vendor supplies. aACE automatically adds new lines to the pending replenishment PO.
The buyer opens the PO based on a daily schedule, maybe an hour before the vendor’s negotiated cut-off time. When a new replenishment is required, it is added to the next pending PO, which will be opened and issued to the vendor the next day.
Automatic inventory replenishment is just one feature of aACE that can help you manage your inventory. Read more about inventory management.