When your orders begin to pour in, your inventory levels may not keep up with the demand. If you struggle with backorder management, your customers could get frustrated and go somewhere else.
aACE’s backorder management tools allow you to label order items as backordered with one click of a button. Depending on your inventory stock and configured preferences, aACE can backorder all the inventory in your order or only designate part of an order as backordered.
Interface Spotlight
The BO flag on an order record allows you to manually mark line items as backordered. If there is some available inventory, aACE asks you if you want to mark the item as entirely backordered or partially backordered.
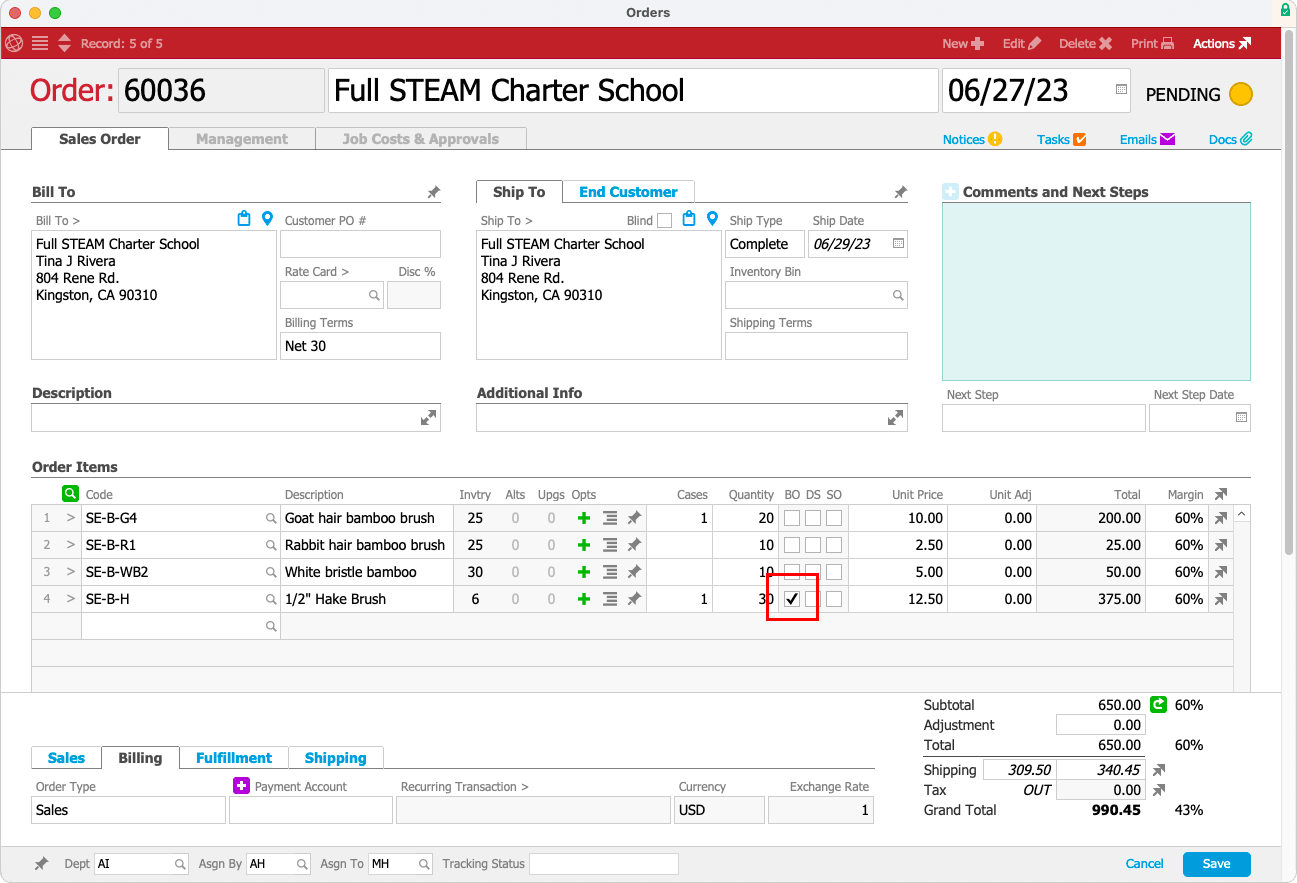
Once the backordered inventory is received, aACE clears the order’s BO flag and automatically generates a shipment for the remaining products. This will notify your warehouse to fulfill the shipment. And, depending on your pre-set preferences, aACE can also simultaneously prompt your sales staff to contact the customer about the status of their backordered items.
Team members can view all backordered items in aACE’s Order Items module. Using aACE’s robust search features, authorized users can view backordered products as well as orders requiring additional inventory for fulfillment.
aACE in Action: Filling Priority Orders
Suppose a business has multiple orders already marked as backordered. Before the next shipment of textbooks comes in from their vendor, they receive a new order for math textbooks from a charter school. Since there are no more books left in the available inventory, all the textbooks are placed on backorder. Typically backorders would be filled on a first-come, first-served basis. In this case, however, the charter school needs the textbooks for the fast-approaching winter term, and they’re willing to pay a rush fee to expedite their order.
The sales member changes the order’s fulfillment priority to Rush 50%, automatically adding a 50% rush fee to the total. The usual lead time for the textbooks is two weeks. The Accounts Payable team emails the PO to the vendor requesting rush delivery.
When the first shipment of textbooks comes in from the vendor a few days later, aACE automatically allocates the new inventory to backorders, first in order of fulfillment priority and then in chronological order. Because the charter school’s order has the Rush 50% fulfillment priority, aACE fills that order first. A shipment is automatically generated to send the ordered textbooks to the charter school.
Backorder management is just one feature of aACE that can help you manage your inventory. Read more about inventory management.