Most businesses experience this at some point or another: orders are pouring in and your inventory can’t quite keep up with the demand. If you can’t manage backorders properly, your customers may get frustrated or go somewhere else.
Fortunately, aACE is here to help. To learn how aACE makes managing backorders easy, let’s follow our fictional company, aACME Education Solutions, as they handle backorders in their day-to-day operations.
To keep the unfortunate occurrence of out-of-stock items to a minimum, aACME has set target balances and replenishment balances on their inventoried items. The target balances tell aACE the maximum number of items that should be kept on their warehouse shelves. The replenishment balances tell aACE when to automatically generate a purchase order to bring the inventory back up. aACME’s textbooks have a target balance of 125 and a replenishment balance of 50.
aACME has 45 math textbooks in stock, with 80 more on order from the publisher. Before that shipment arrives, the sales department receives an order from the Montboro School District for 50 math textbooks. When Account Manager Mara Harvey enters the 50 textbooks into the order, a dialog box pops up informing her that the quantity exceeds the available inventory.
Mara could choose to put all 50 textbooks on backorder so that the entire order will be filled once the inventory is replenished. She also has the option of splitting the line item so the customer receives some of the items from the current inventory, with the rest placed on backorder. She calls her contact, Sam Patel, at Montboro to explain the situation; with all the necessary information at her fingertips in aACE, she’s able to present Sam with all of his options. Sam lets Mara know that they are not in a rush but that they’ll take as many textbooks as they can now and the rest when they’re back in stock.
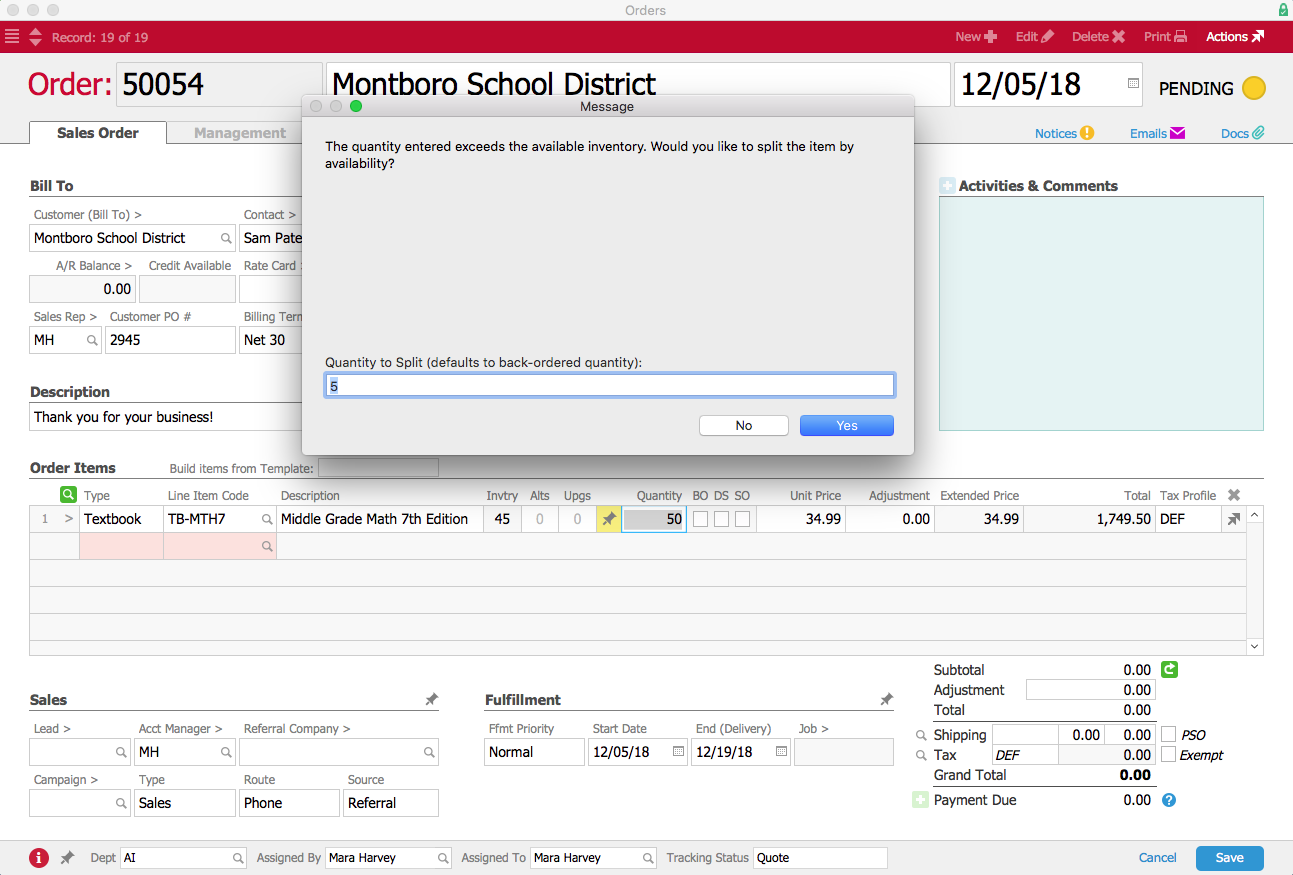
Mara clicks ‘Yes’ to split the order based on the available inventory. aACE automatically updates the quantity of the textbooks in the first line item to 45 and creates a second line item for the remaining 5. This second line item is marked with the backorder (“BO”) flag, and aACE automatically generates an outgoing shipment for the 45 textbooks in stock.

But what happens when another order is placed for the same product?
Before the next shipment of textbooks comes in from the vendor, Mara receives another order for 80 math textbooks from the Full STEAM Academy Charter School. Since there are no more books left in the available inventory, all 80 textbooks are placed on backorder. Typically backorders would be filled on a first-come, first-served basis. In this case, however, the Full STEAM Academy needs the textbooks for the fast-approaching winter term, and they’re willing to pay a rush fee to expedite their order.
Mara changes the order’s fulfillment priority to Rush 50%, automatically adding a 50% rush fee to the total. Since the 80 backordered textbooks from the Full STEAM Order plus the 5 backordered textbooks from the Montboro order will use up all of the inventory that’s currently on order from the publisher, aACE automatically generates a purchase order for 130 textbooks to bring the available inventory back up to its target balance.
The typical lead time for the textbooks is two weeks from the time the Accounts Payable department emails the PO to the vendor to the time the new stock arrives in aACME’s warehouse. When the first shipment of 80 textbooks comes in from the publisher a few days later, aACE automatically allocates the new inventory to backorders, first in order of fulfillment priority and then in chronological order. Because the Full STEAM Academy’s order has the Rush 50% fulfillment priority, aACE fills that order first. A shipment is automatically generated to send 80 textbooks to that school.
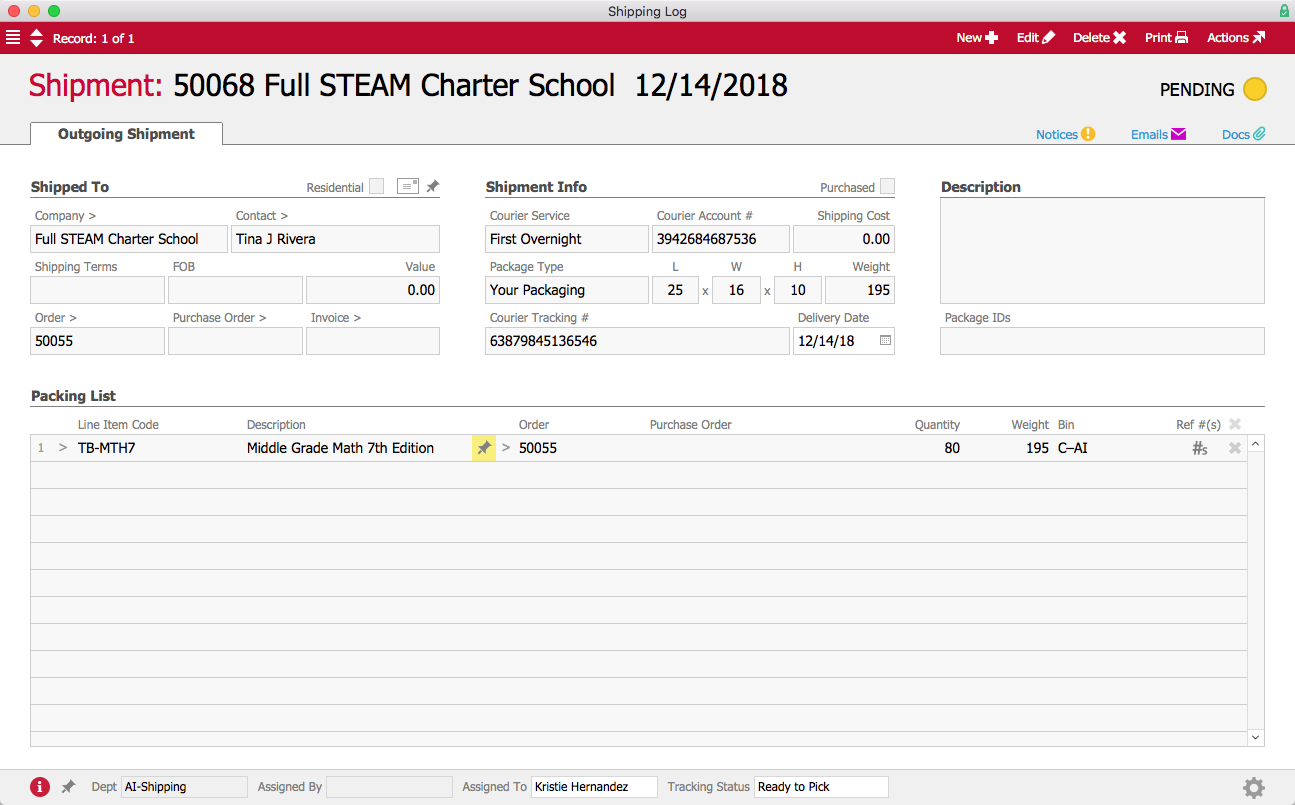
Two weeks later, the shipment of 130 textbooks comes in. With the rush order completed, aACE generates a shipment for the Montboro School District’s 5 backordered textbooks. This brings the available inventory to the target balance of 125, with no additional POs outstanding.
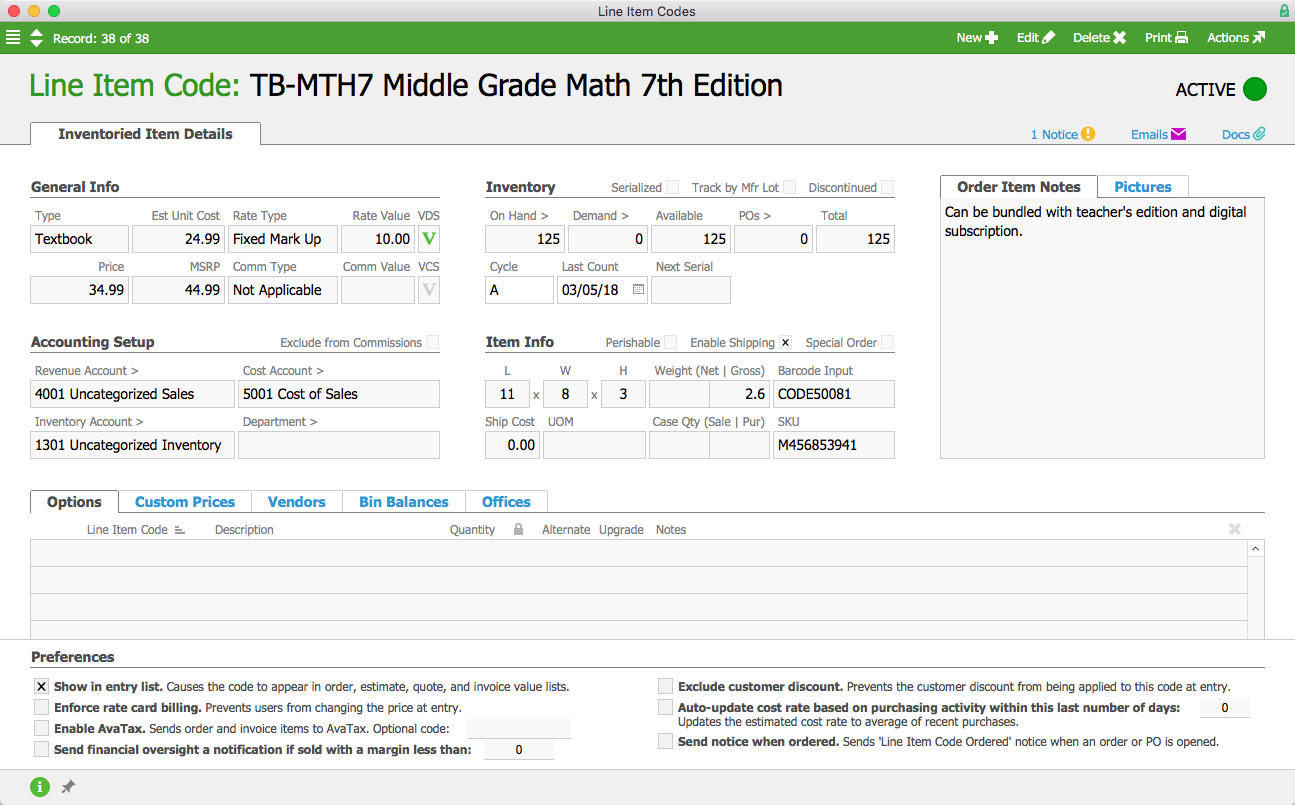
The table below illustrates the movement of inventory throughout this example, using red and green arrows to indicate the values that have changed with each event.
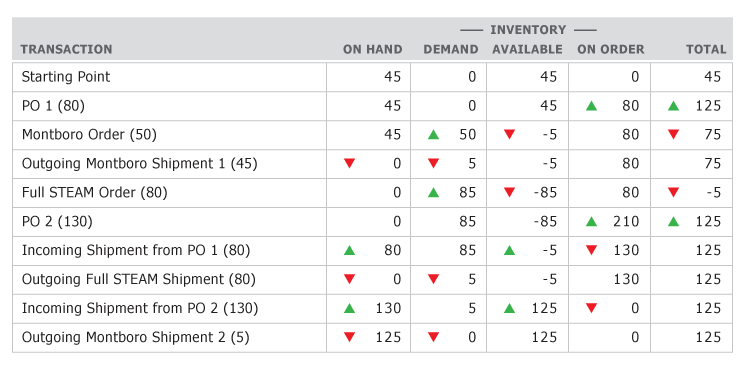
If the managers at aACME want to see what items are on backorder, aACE offers different ways to access that information. In the Order Items module, they can quickly pull up a list of all backordered items, with links to the associated orders. Likewise, from the Line Item Codes module they can review backorders for a specific item, like the math textbook; aACE makes it easy to view a list of the orders placing demand on that item’s inventory with just one click.
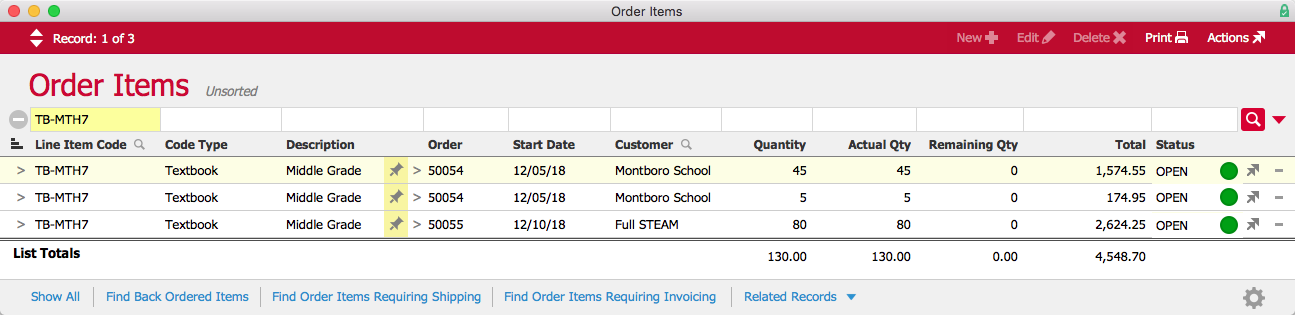
aACE streamlines backorder management, keeping your business moving and your customers happy. Now that we’ve seen what it’s done for our fictional company, take a look at our Southwest Auto Accessories success story to learn how this feature helped a real aACE client gain visibility into their backorder process.